Tryptophan Analysis
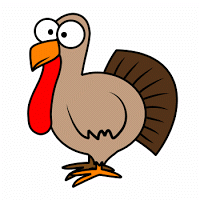
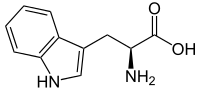
Fatigue crack propagation testing provides users information about the resistance of a material to crack initiation and propagation under cyclical loading. Currently, ASTM E647 is used to monitor the crack propagation behavior of plastic and metallic materials. Engineers at Cambridge Polymer Group have developed an automated optical system that allows real-time assessment of crack length during a fatigue crack test. Two laboratories compared test results using this optical system on UHMWPE samples, with the results presented at the 7th Annual UHMWPE conference in Philadelphia, PA in October 2015. The presentation can be found here.
The third edition of the UHMWPE Biomaterials Handbook was just offered for purchase. This edition contains the history of ultra high molecular weight polyethylene and its use in hip and knee arthroplasty. The new edition contains multiple chapters addressing analytical testing techniques to characterize UHMWPE, wear testing, accelerated aging, antioxidant effects, and advances in UHMWPE processing and formulation development. CPG researchers Braithwaite, Kozak, and Spiegelberg contributed a chapter on characterization techniques on UHMWPE, including details on fatigue crack propagation testing, true stress-true strain measurements, and electron spin resonance spectroscopy.
Link to purchase 3rd edition of the UHMWPE Handbook
BE: Please provide a brief overview of Cambridge Polymer Group and the services you provide.
SS: We like to think of ourselves as a one-stop resource for our clients, working everywhere in the product lifecycle from concept through launch and (hopefully not) root-cause analysis.
We are a well-established contract research laboratory that has been operating since the mid-1990’s specializing in polymer science. Our scientists are experienced in analytical testing, polymer chemistry, and product development, testing and analysis. We often serve as either an external routine analytical testing laboratory, or an external research and development facility for our clients.
BE: What does rheological testing involve?
SS: Rheology is the study of the flow of matter. Most people are familiar with the concept of viscosity, and how it relates to how easy it is to pour or spread liquids. Viscosity is one of the parameters that comes out of rheological characterization, but we do much more than that.
We can determine the viscoelastic nature of material, which tells you how the material will respond to different rates of deformation, which is important in polymer processing and end use. We can also (almost uniquely) characterize the response of fluids to extensional deformation, such as found in fibre spinning, coating or injection molding.
BE: What type of materials can you test?
SS: Polymers are, of course, our main source of testing, but the word ‘polymer’ extends beyond standard synthetic polymers. We do a lot of testing of natural polymers, such as collagen and hyaluronic acid, as well degradable polymers.
These polymers can be on their own, or as blends or composites, or functionally part of a larger device, so you can see that the scope of devices and products that “polymers” covers is far broader than the image that “plastics” alone might conjure up.
In the medical field, we also do a fair amount of testing on the cleanliness of devices, which can include both polymeric and metallic devices. In particular, in rheological testing we can of course test the melt-flow properties of the base resins, but we also have extensive experience in understanding and testing the solution and blend properties of these high molecular weight materials.
The rich and varied response of polymers in solution makes for challenging rheological testing, and understanding the end-use and requirements of the test is critical to get useful results.
Link to full Azom Interview
A Workshop on Reprocessing of Re-usable Medical Devices will be held Tuesday, November 15, 2016. Sponsored by ASTM Committee F04 on Medical and Surgical Materials and, the workshop will be held at the Renaissance Orlando at SeaWorld in Orlando, FL, in conjunction with the November standards development meetings of the committee.
Objectives:
A recent article in Medical Processing Outsourcing (June 2, 2015) estimates that reprocessed medical devices will grow by 19% annually to reach $2.58 billion in 2020. A key element of this successful growth is assurances of cleanliness and safety standards.
Recently, the FDA released a guidance document on reprocessing of reusable devices (March 12, 2015) and held a public meeting on May 14-15, 2015 to discuss infections associated with the use of duodenscopes.
The workshop is intended to bring thought leaders together on the issues involving cleaning of re-usable medical devices to determine the areas of standardization that ASTM should focus on in the next few years.
Topics to be discussed include the following:
1. History of reprocessing issues
2. Review of relevant existing ASTM, ISO, AAMI, and FDA standards/documents
3.Designing of medical devices for reprocessing
4.Reprocessing
5. Testing for biological residues
6. Sterilization of residual soil
7. Biocompatibility of residual soil/limits
8. Discussion of new standards development for ASTM to consider
Please contact CPG researcher and workshop co-chair Stephen Spiegelberg with any questions or to submit an abstract.
More details on the workshop can be found on the ASTM web site.
Ultra high molecular weight polyethylene (UHMWPE) is commonly used as a bearing surface in hip, knee, shoulder, and other total joint replacement arthroplasties. Aging of UHMWPE that has been irradiated without additional treatment to stabilize the residual free radicals can result in oxidation followed by chain scissioning. Researchers will usually measure oxidation index to characterize shelf‐life, but this technique does not capture the actual degradation due to oxidation. In this study, gamma sterilized UHMWPE was accelerated aged, and the molecular weights of extractable material
were characterized with gel permeation chromatography in an attempt to see if this technique can be used to characterize shelf life of the aged material.
The extraction of the polyethylene material in this study shows that there is a molecular weight difference between the unaged and aged material, with the aged material showing broadening in the molecular weight distribution. This change can be explained by oxidative degradation, which is supported by the oxidation index. The test methodology shows that a larger ratio of solvent to sample is required to ensure extraction without gelation of the extracted material, and that 4 hours is sufficient to extract the larger molecular weight species. The impact of the molecular weight change on in vivo performance, however, cannot be discerned from this test.
See the poster presented at the Orthopedic Research Society in March, 2015 here.